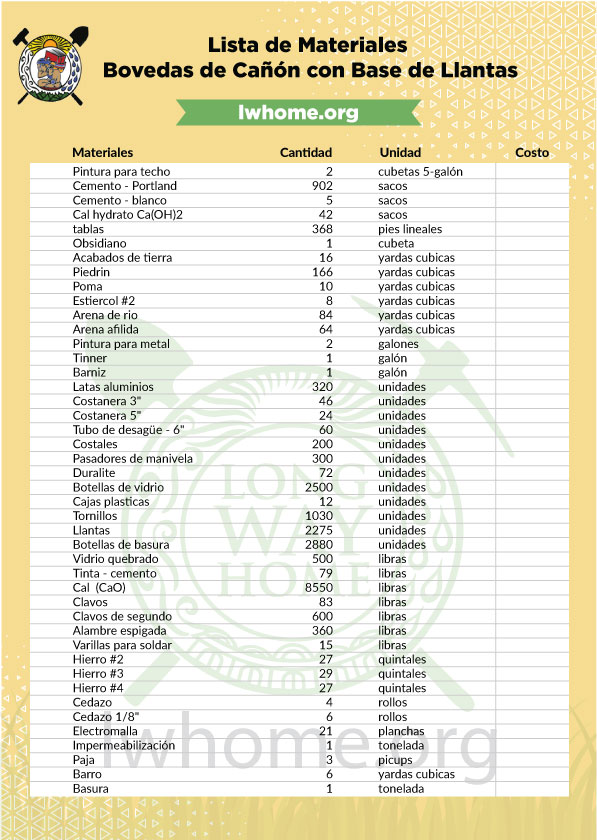
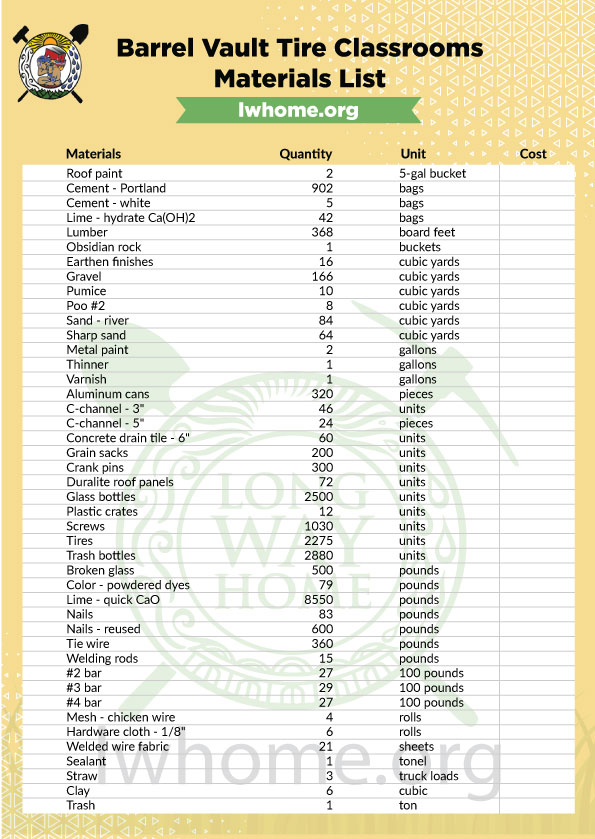
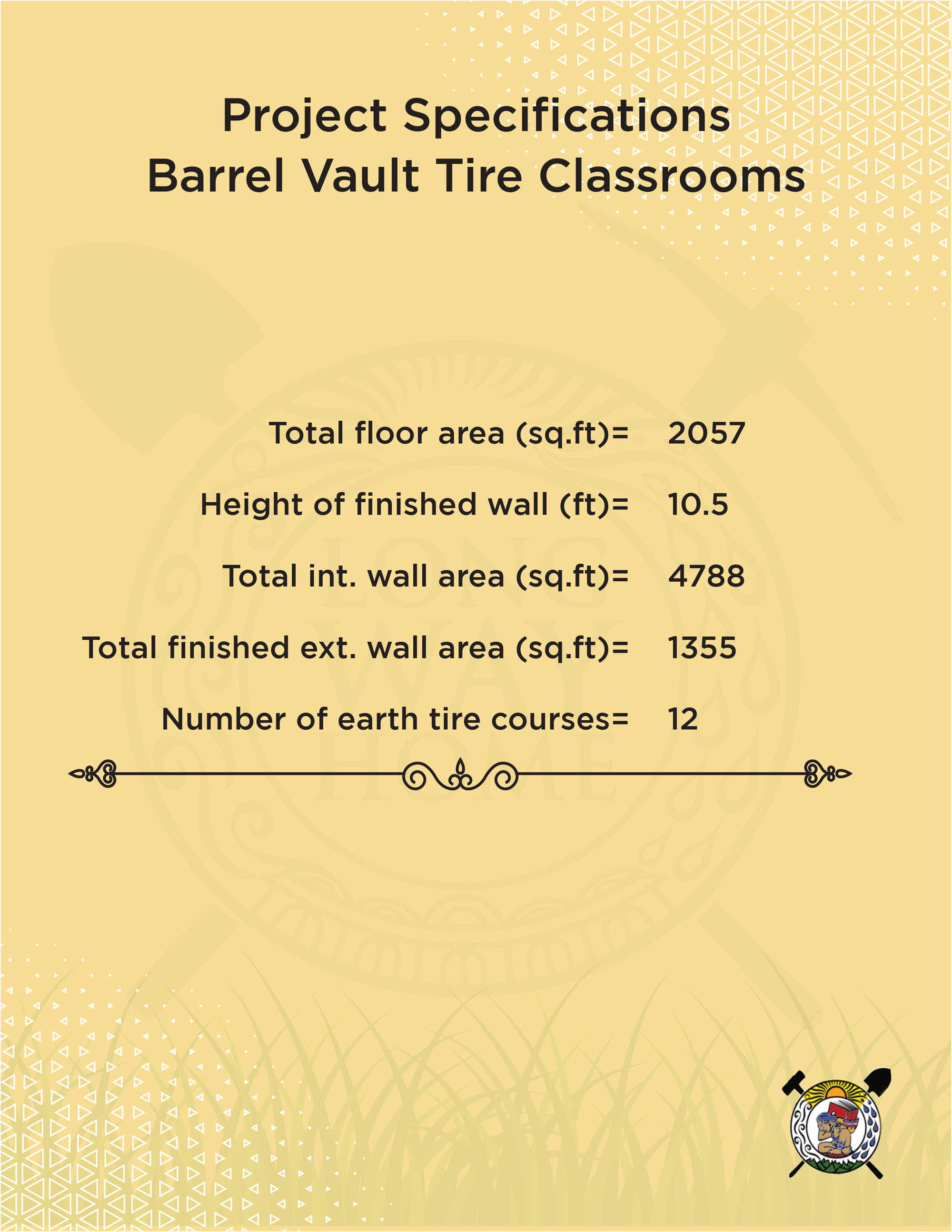
The primary structure is made of walls of packed tires laid out on a 105’ x 30’ footprint. Tire walls are 10’ tall and follow curved patterns creating a geometrically stable shape where no buttressing is needed. In addition, it allows to avoid the presence of sharp corners where stresses would accumulate in the event of an earthquake, thus creating weak spots in the structure.
Tires are filled with the earth taken out during the excavation stage, and non-biodegradable waste. The tires are stacked in a running-bond pattern to maximize interlocking between courses. Additionally, horizontal rebars are laid between two courses about halfway up the wall in order to stiffen it against lateral forces during the construction stage. A 6” deep concrete bond beam is poured on top of the last course of tires in order to tie the whole primary structure together and facilitate the connection with the concrete roof.
Walls are founded on 2’ x 2’ trenches, filled with tamped down gravel. The gravel keeps the lowest course of the walls dry and allows any moisture below the wall to drain down into the ground.
The ground floor slab (both inside and outside) is a 6” thick concrete slab poured on top of a layer of gravel to avoid any contact between the concrete and ground water. On its South edge, the patio slab stops at a 4’ tall rammed earth tire retaining wall. The central room of the building presents an additional floor 9’ higher than the ground floor slab made out of wooden planks supported by concrete beams tied into the bond beam.
The roof of each individual room consists of a reinforced concrete vault tied into the bond beam. Glass bottles cut in half are tied into the reinforcement and act as skylights. The patio roof is made with paper-cement fiber corrugated panels supported by metal rafters and purlins which rest on the bond beam and 12 outdoor concrete columns laid along the South edge of the buildings.
Door frames are made with concrete columns carrying concrete arches. The columns are founded on square footings and cast against the tires, providing lateral restraint to the walls. The concrete arches are tied into the bond beam to limit the impact of door openings on the global stability of the structure.
Window openings in the tire walls are made of earth bags and follow the geometrically-stable arch shape to avoid the presence of lintels. The openings above the bond beam and under the roof arch are filled in with a glass-brick (glass bottles cut in half and taped together) wall supporting a metal framed window.
Wall finishes (interior and exterior) are made of cob (earth + sand +straw) applied against the tire walls where nails have been added to enhance the cob adherence. The cob fills in the voids between tires and creates a flat surface. It is covered by two layers of plaster: a form coat (cement + lime + coarse sand) and a final coat (cement + lime + fine sharp sand).
The interior ceiling plasters are the same as those used on the walls. Exterior ceiling plaster consists of cement-based render and sealant paint with the exception of the central room where a 3” thick layer of pumice-crete (cement + pumice aggregate) is added in order to thermally insulate the first floor room.
Rainwater is collected on the concrete roof through awnings and sculpted gutters that guide water towards a 4,000-gallon water cistern located at the Northwest corner of the building. The cistern then supplies water for all the sinks and the shower of the building. In addition, even though it is mostly covered, the patio slab is sloped towards a drain swale located at the South side of the building where water crosses the South retaining wall.
Barrel Vault Tire Classrooms
The primary structure is made of walls of packed tires laid out on a 105’ x 30’ footprint. Tire walls are 10’ tall and follow curved patterns creating a geometrically stable shape where no buttressing is needed. In addition, it allows to avoid the presence of sharp corners where stresses would accumulate in the event of an earthquake, thus creating weak spots in the structure.
Tires are filled with the earth taken out during the excavation stage, and non-biodegradable waste. The tires are stacked in a running-bond pattern to maximize interlocking between courses. Additionally, horizontal rebars are laid between two courses about halfway up the wall in order to stiffen it against lateral forces during the construction stage. A 6” deep concrete bond beam is poured on top of the last course of tires in order to tie the whole primary structure together and facilitate the connection with the concrete roof.
Walls are founded on 2’ x 2’ trenches, filled with tamped down gravel. The gravel keeps the lowest course of the walls dry and allows any moisture below the wall to drain down into the ground.
The ground floor slab (both inside and outside) is a 6” thick concrete slab poured on top of a layer of gravel to avoid any contact between the concrete and ground water. On its South edge, the patio slab stops at a 4’ tall rammed earth tire retaining wall. The central room of the building presents an additional floor 9’ higher than the ground floor slab made out of wooden planks supported by concrete beams tied into the bond beam.
The roof of each individual room consists of a reinforced concrete vault tied into the bond beam. Glass bottles cut in half are tied into the reinforcement and act as skylights. The patio roof is made with paper-cement fiber corrugated panels supported by metal rafters and purlins which rest on the bond beam and 12 outdoor concrete columns laid along the South edge of the buildings.
Door frames are made with concrete columns carrying concrete arches. The columns are founded on square footings and cast against the tires, providing lateral restraint to the walls. The concrete arches are tied into the bond beam to limit the impact of door openings on the global stability of the structure.
Window openings in the tire walls are made of earth bags and follow the geometrically-stable arch shape to avoid the presence of lintels. The openings above the bond beam and under the roof arch are filled in with a glass-brick (glass bottles cut in half and taped together) wall supporting a metal framed window.
Wall finishes (interior and exterior) are made of cob (earth + sand +straw) applied against the tire walls where nails have been added to enhance the cob adherence. The cob fills in the voids between tires and creates a flat surface. It is covered by two layers of plaster: a form coat (cement + lime + coarse sand) and a final coat (cement + lime + fine sharp sand).
The interior ceiling plasters are the same as those used on the walls. Exterior ceiling plaster consists of cement-based render and sealant paint with the exception of the central room where a 3” thick layer of pumice-crete (cement + pumice aggregate) is added in order to thermally insulate the first floor room.
Rainwater is collected on the concrete roof through awnings and sculpted gutters that guide water towards a 4,000-gallon water cistern located at the Northwest corner of the building. The cistern then supplies water for all the sinks and the shower of the building. In addition, even though it is mostly covered, the patio slab is sloped towards a drain swale located at the South side of the building where water crosses the South retaining wall.
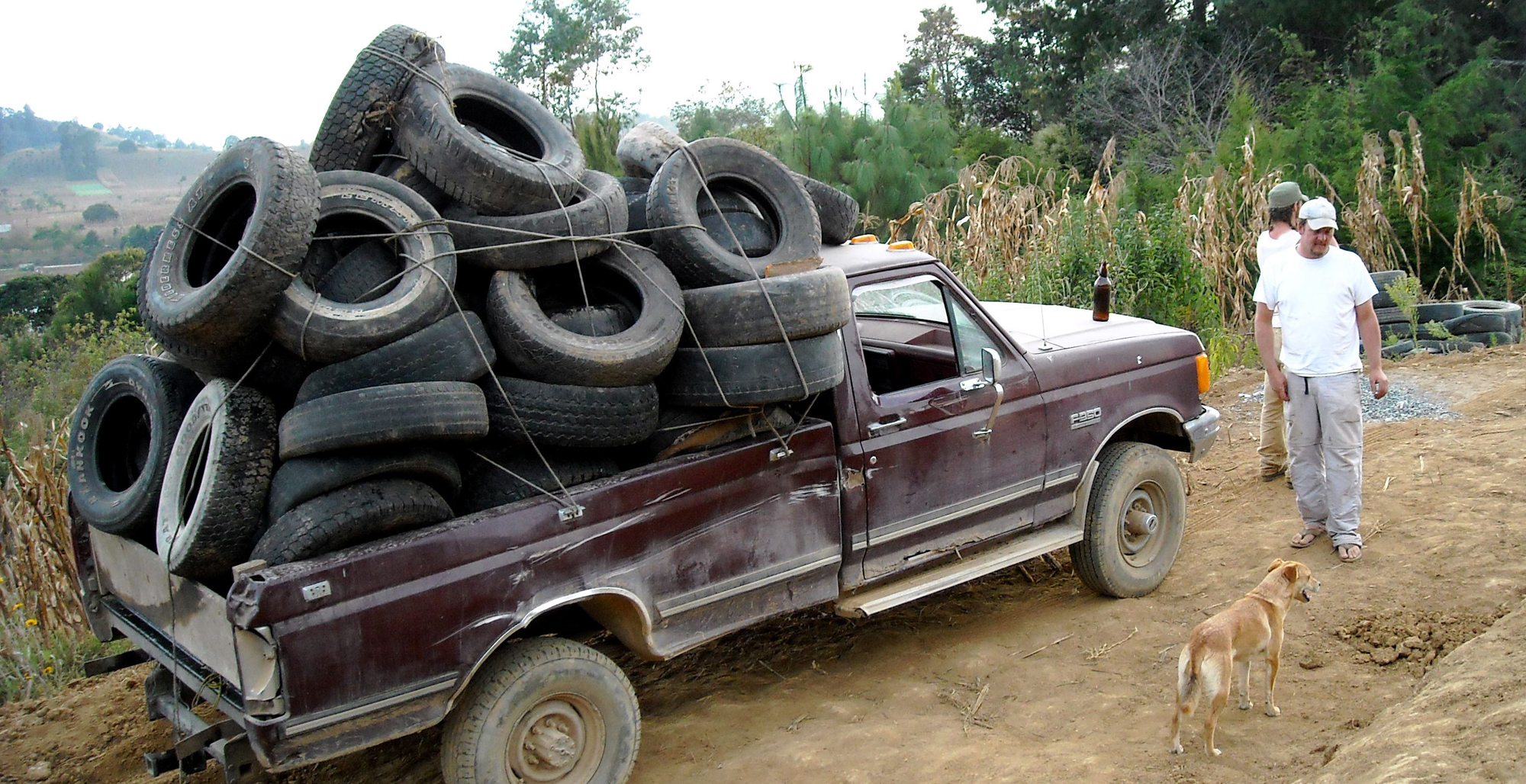
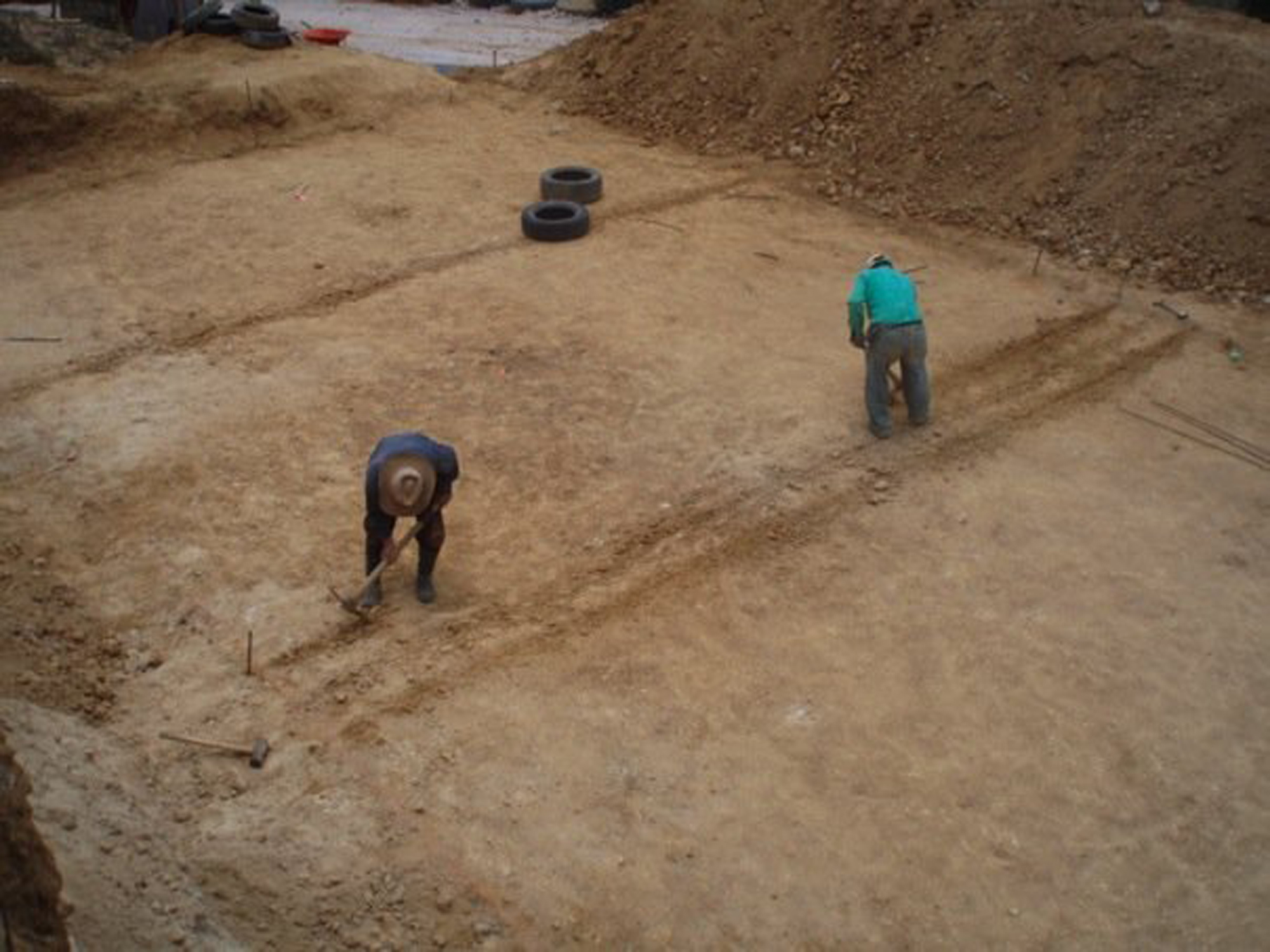
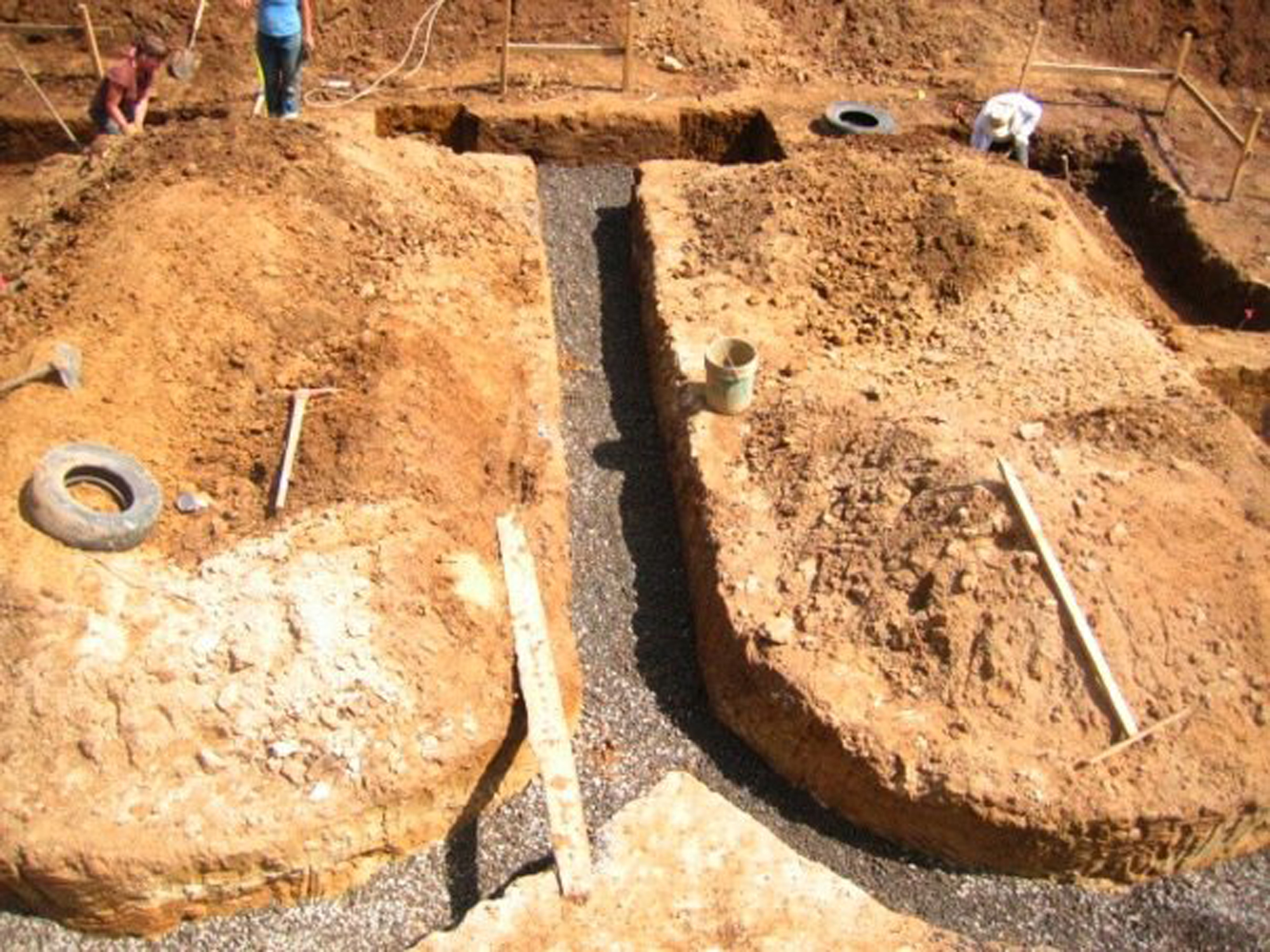
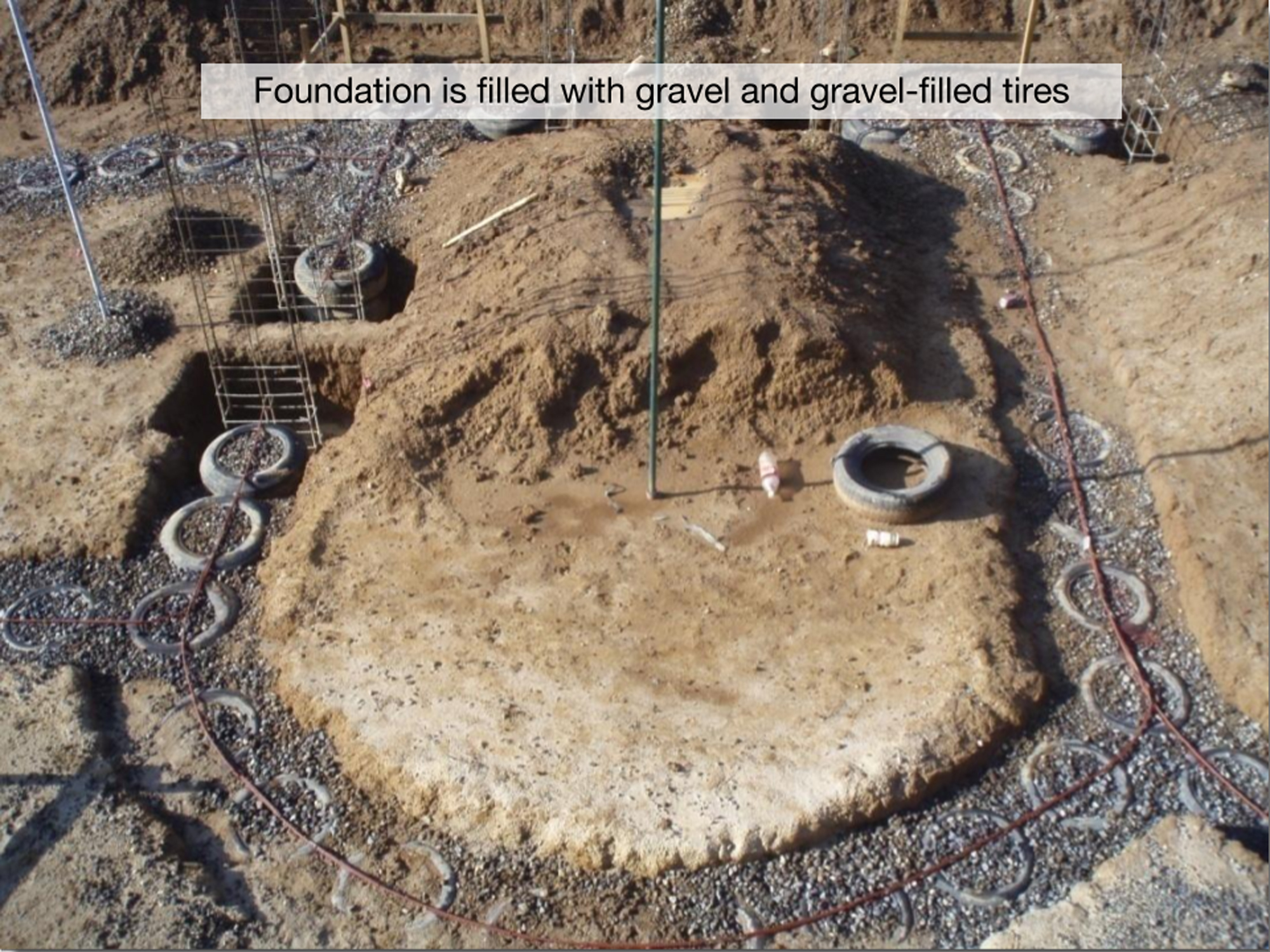
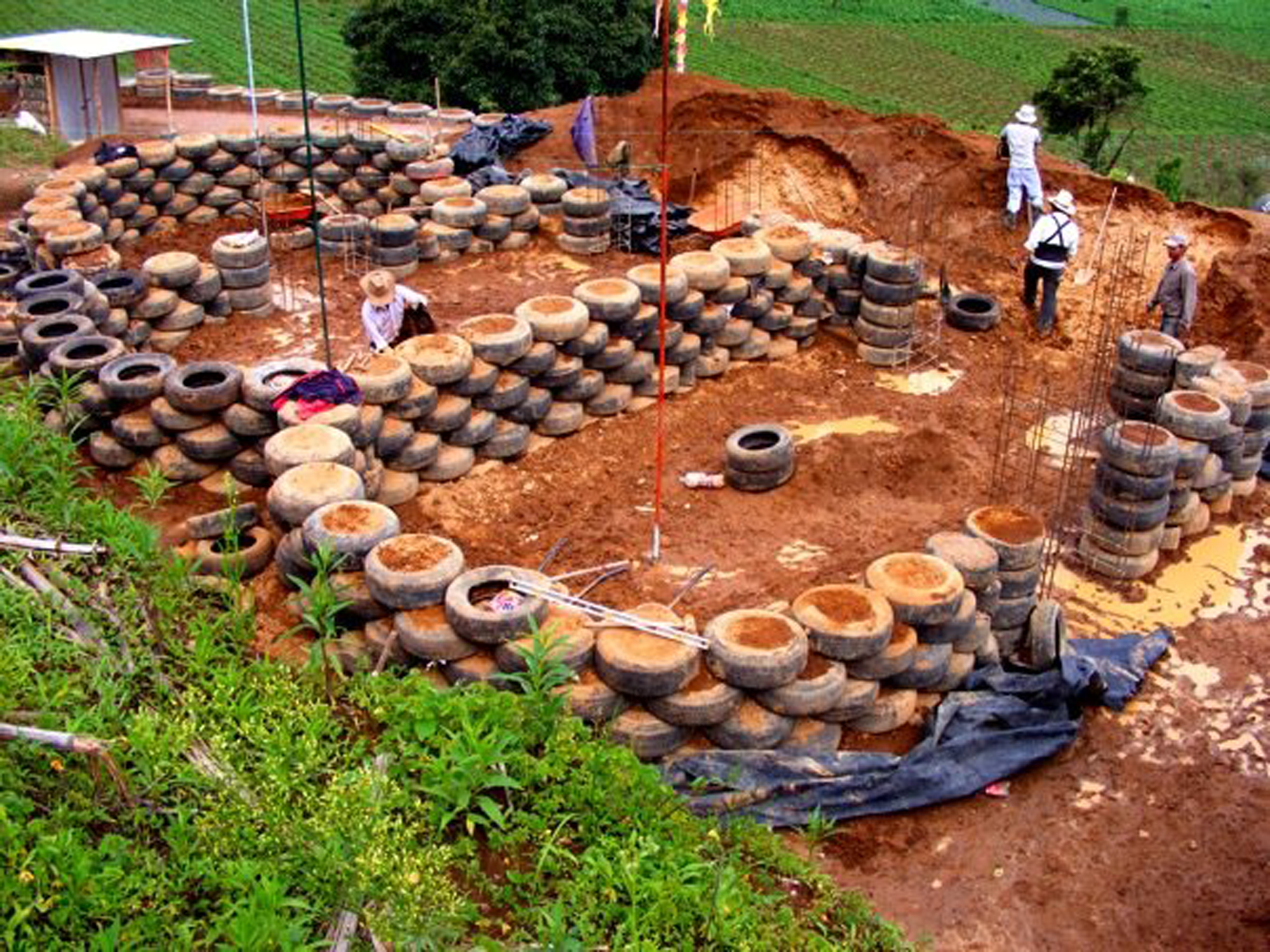
.jpg)
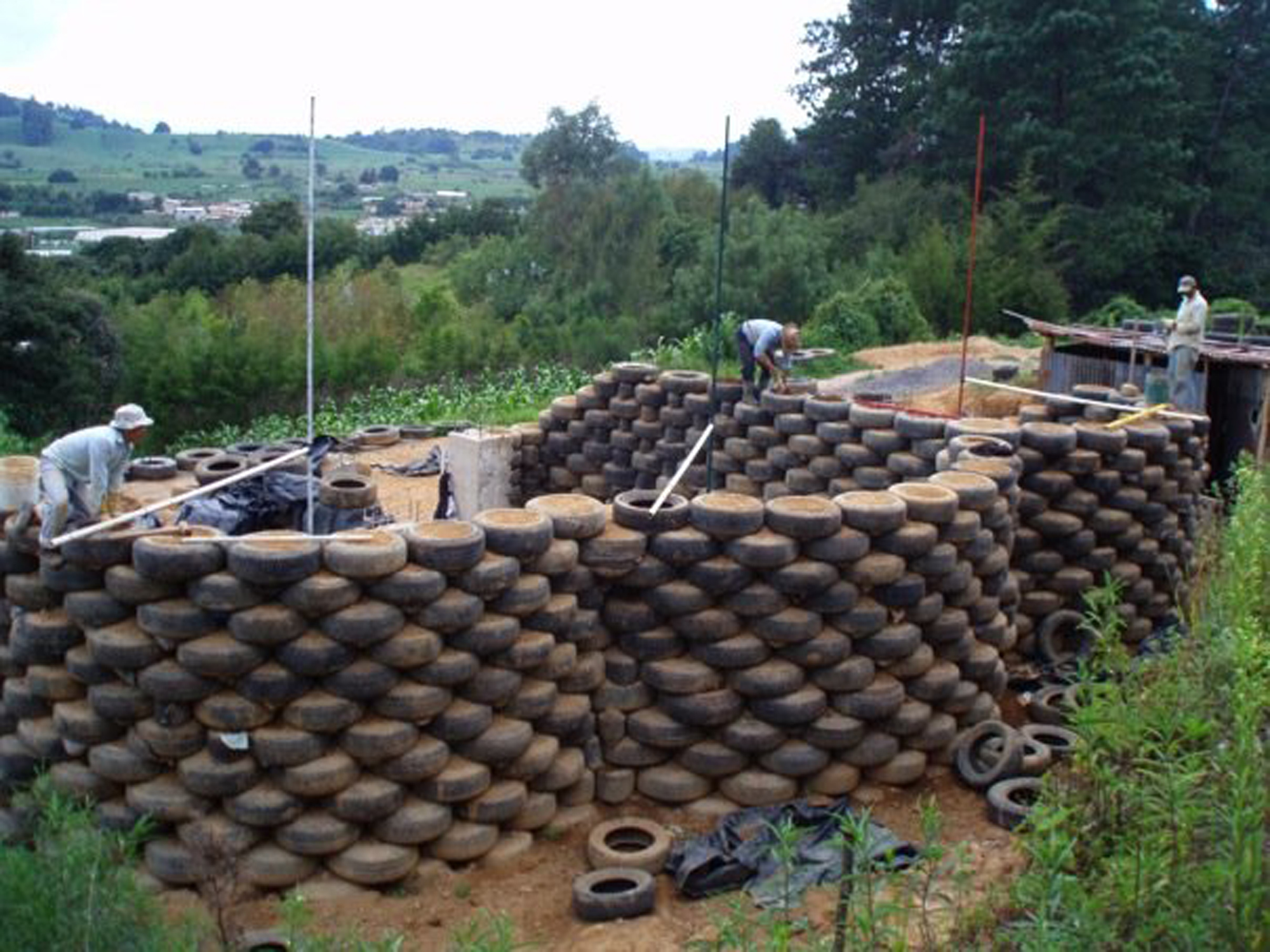
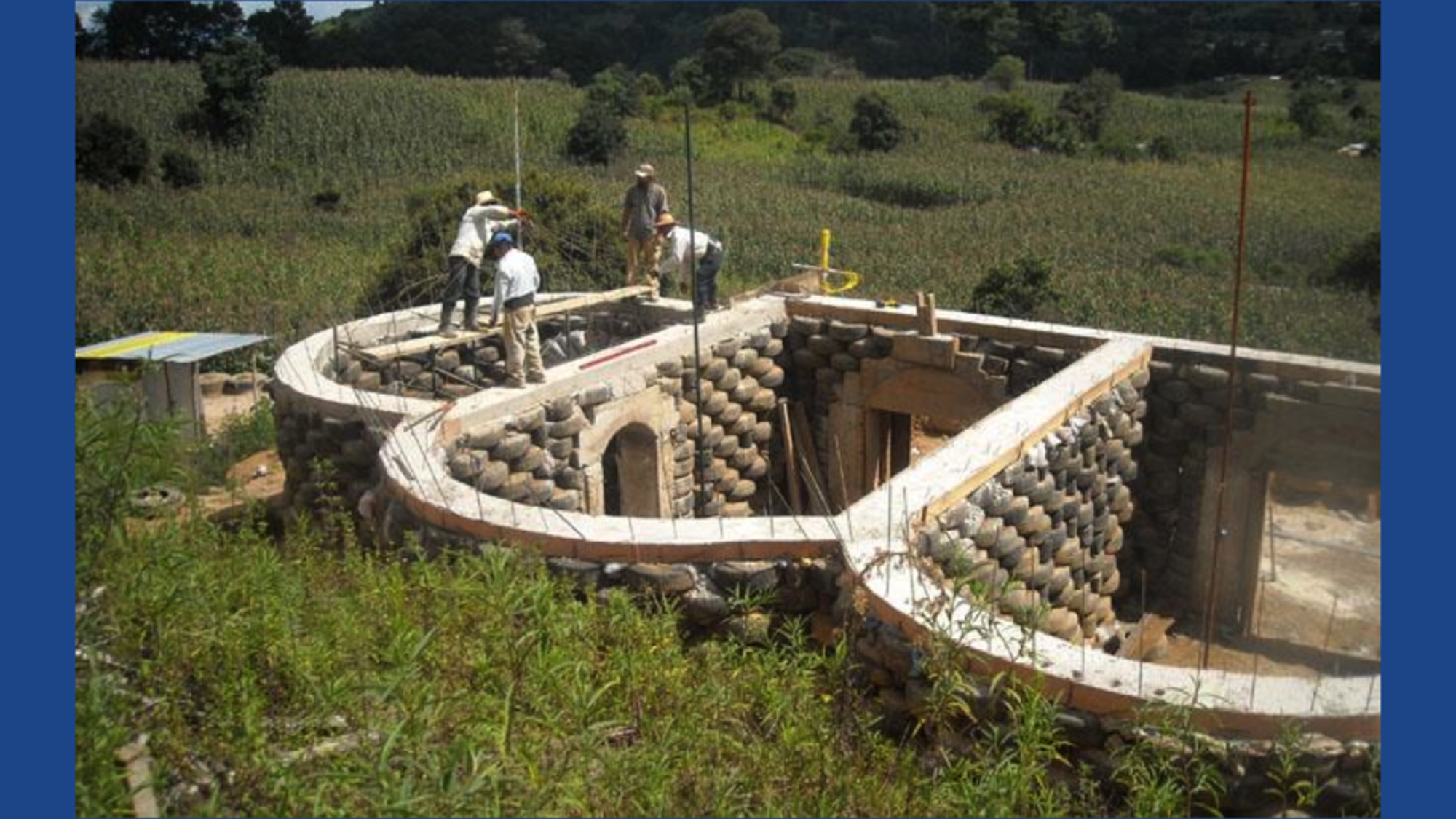
.jpg)
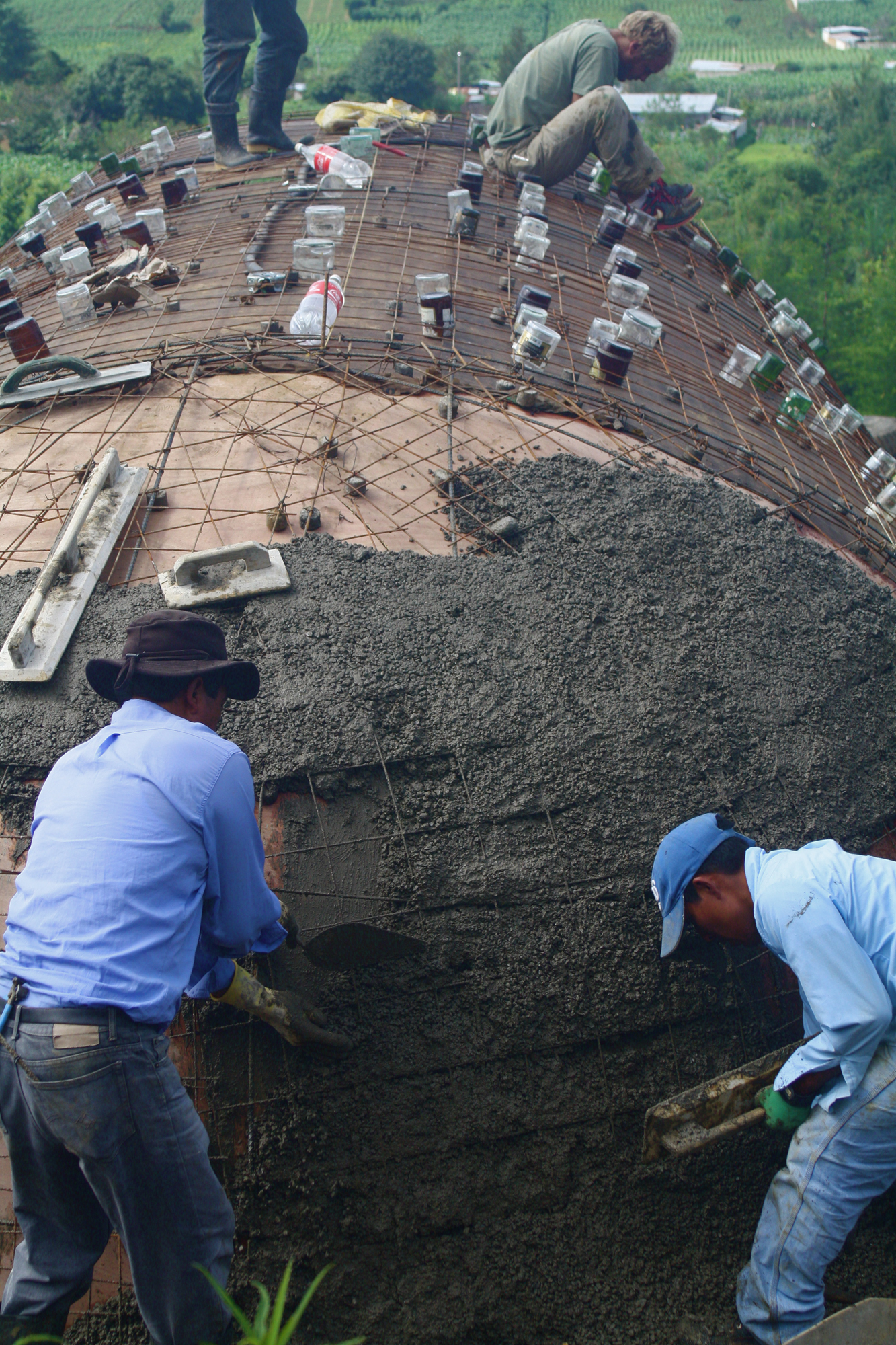
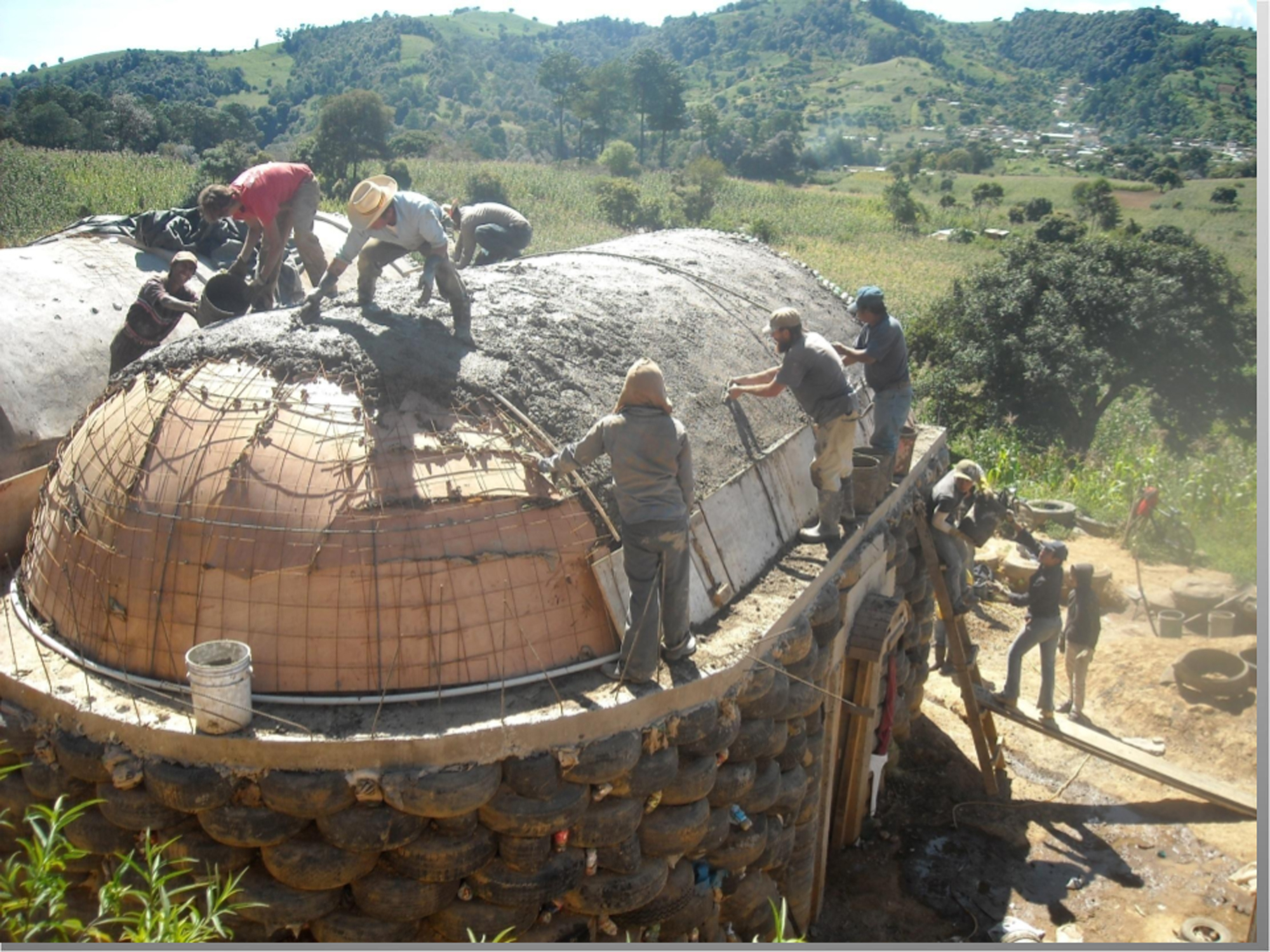
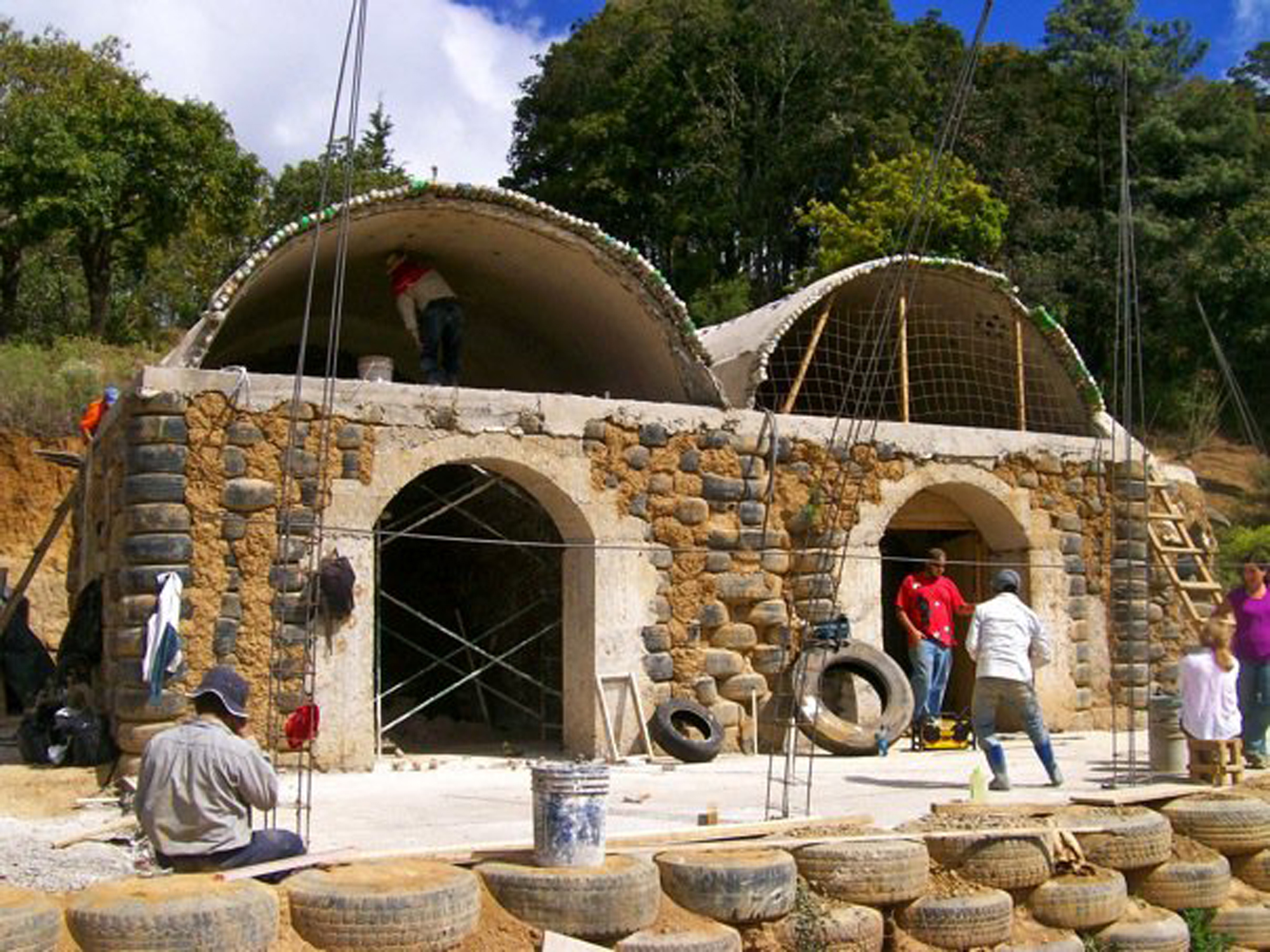
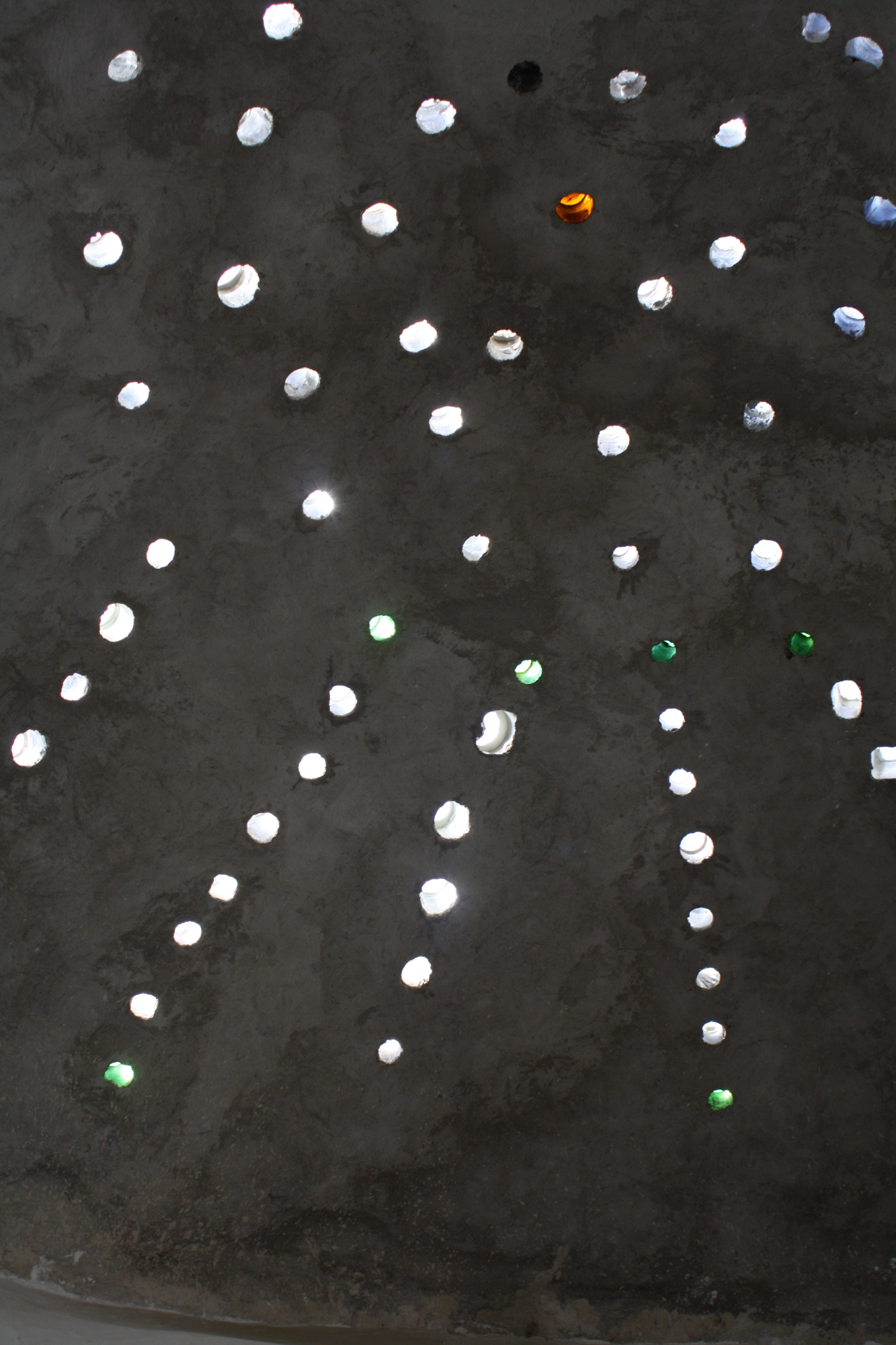
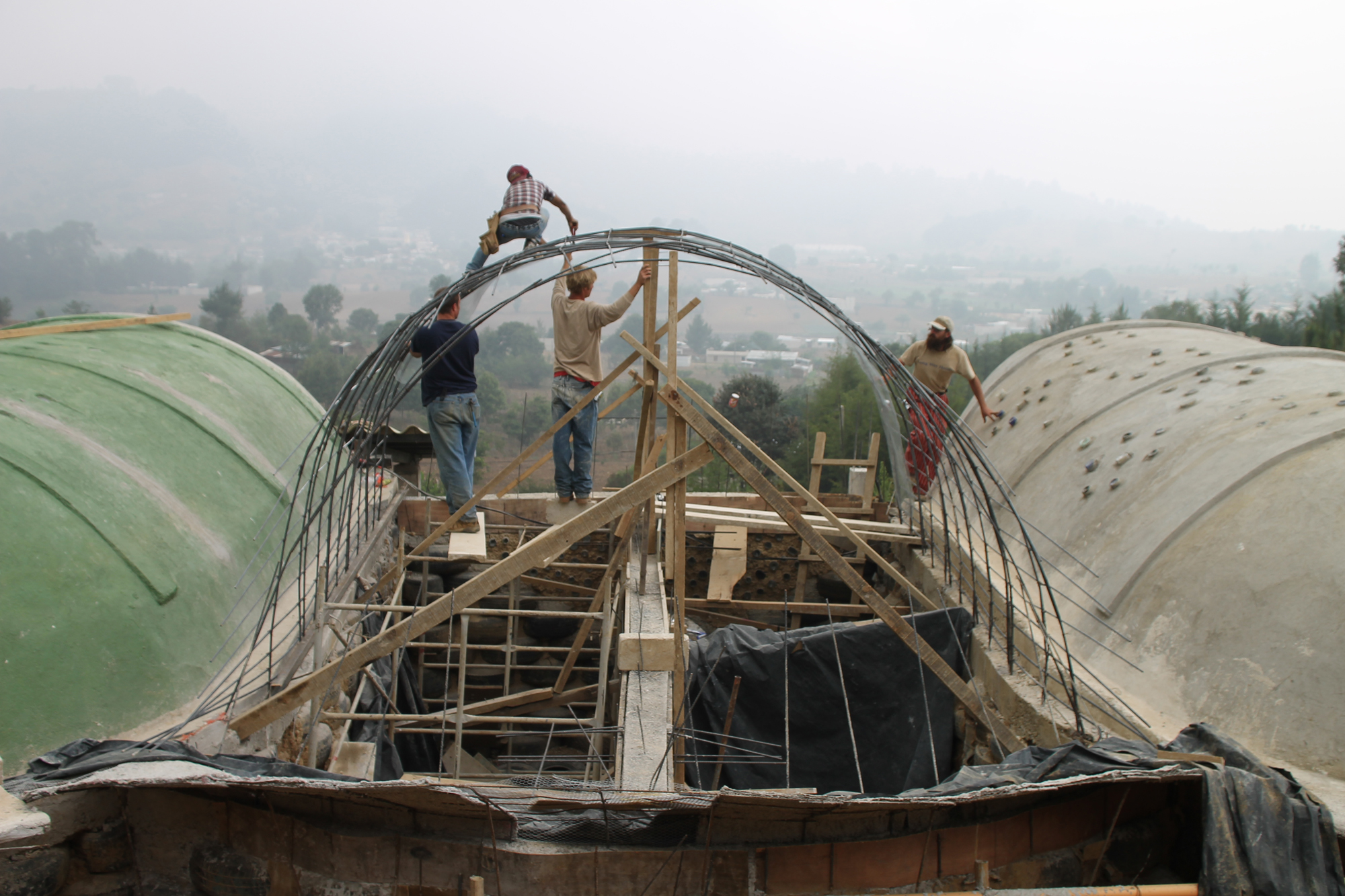
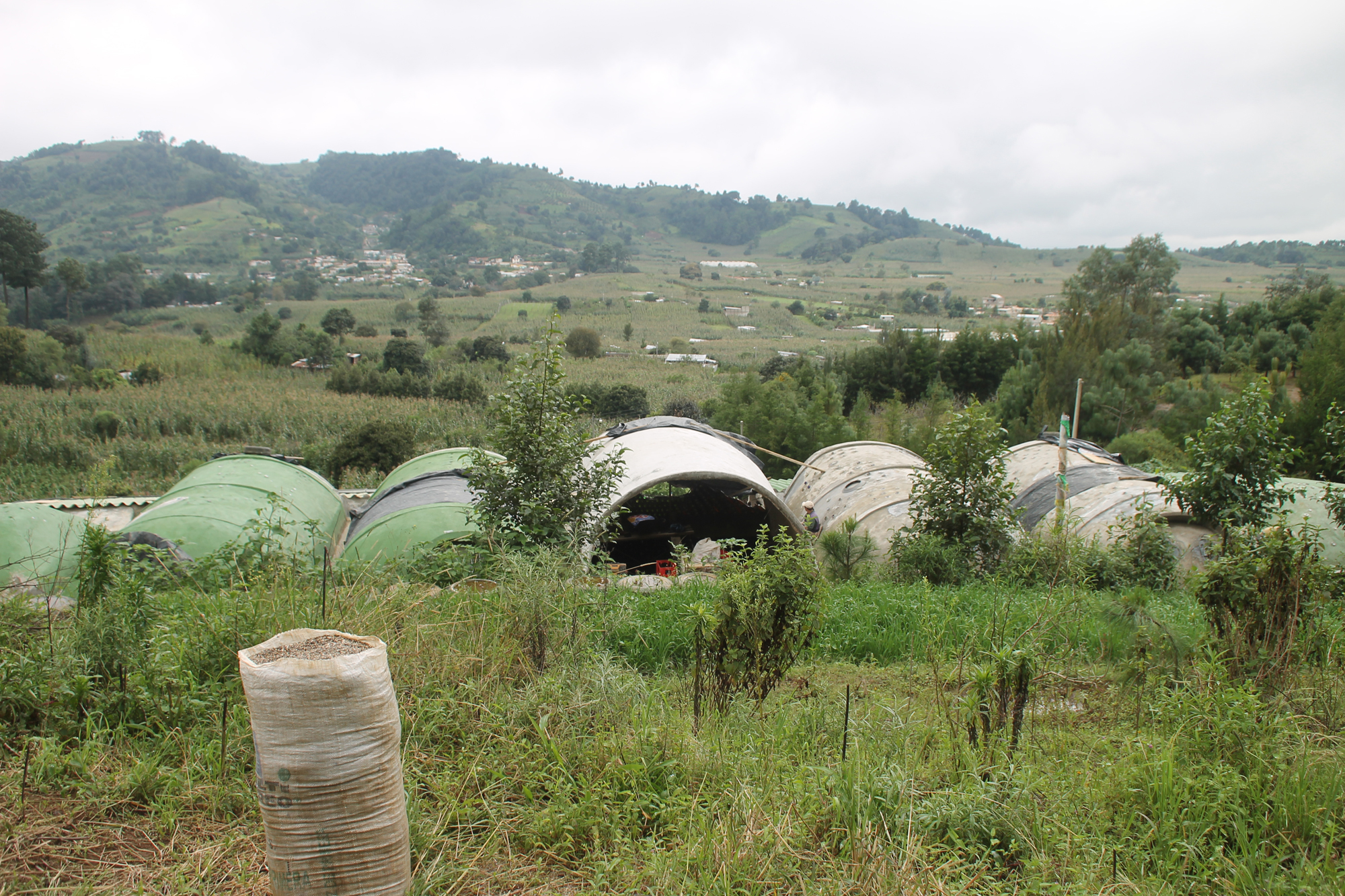
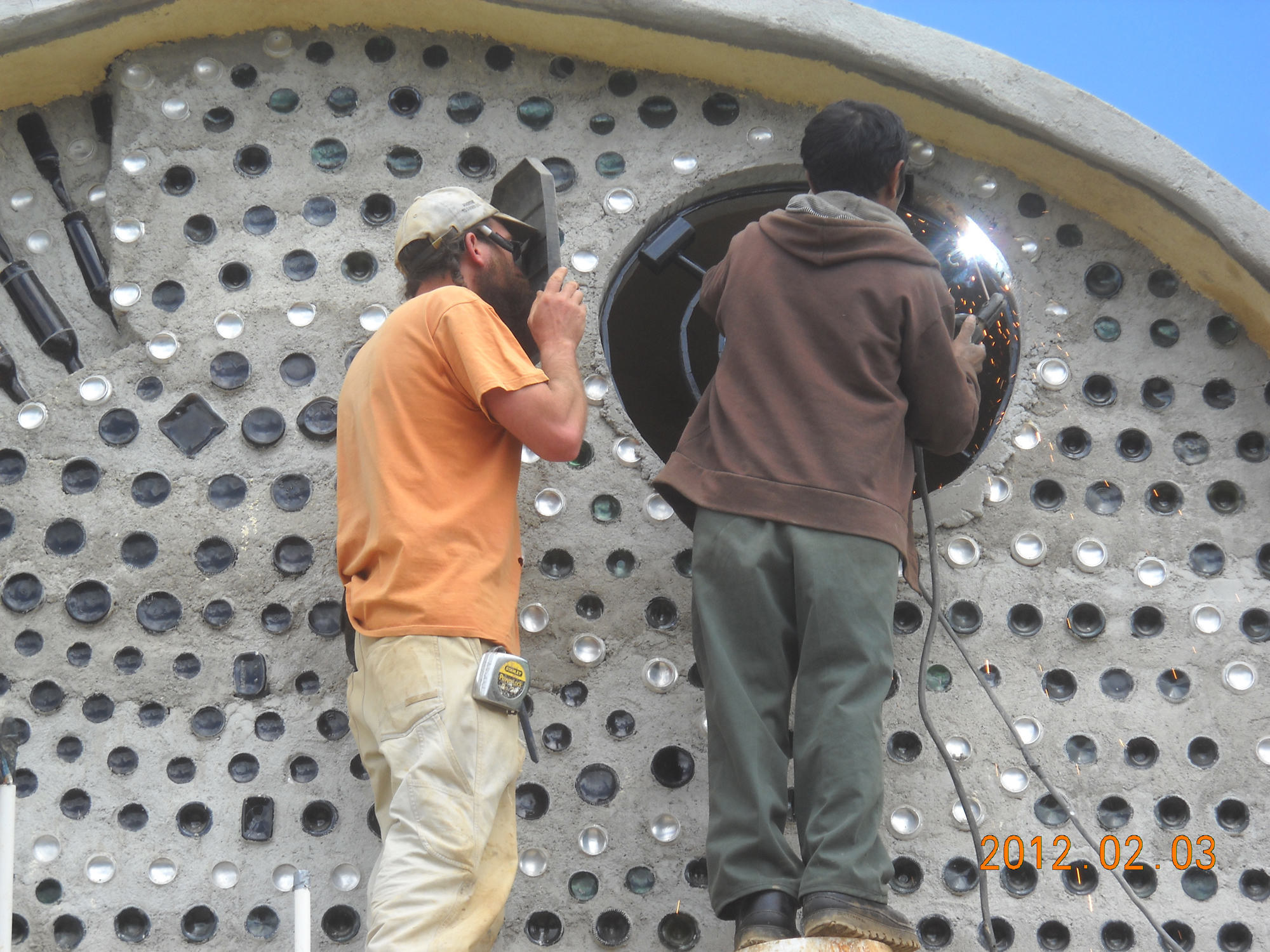
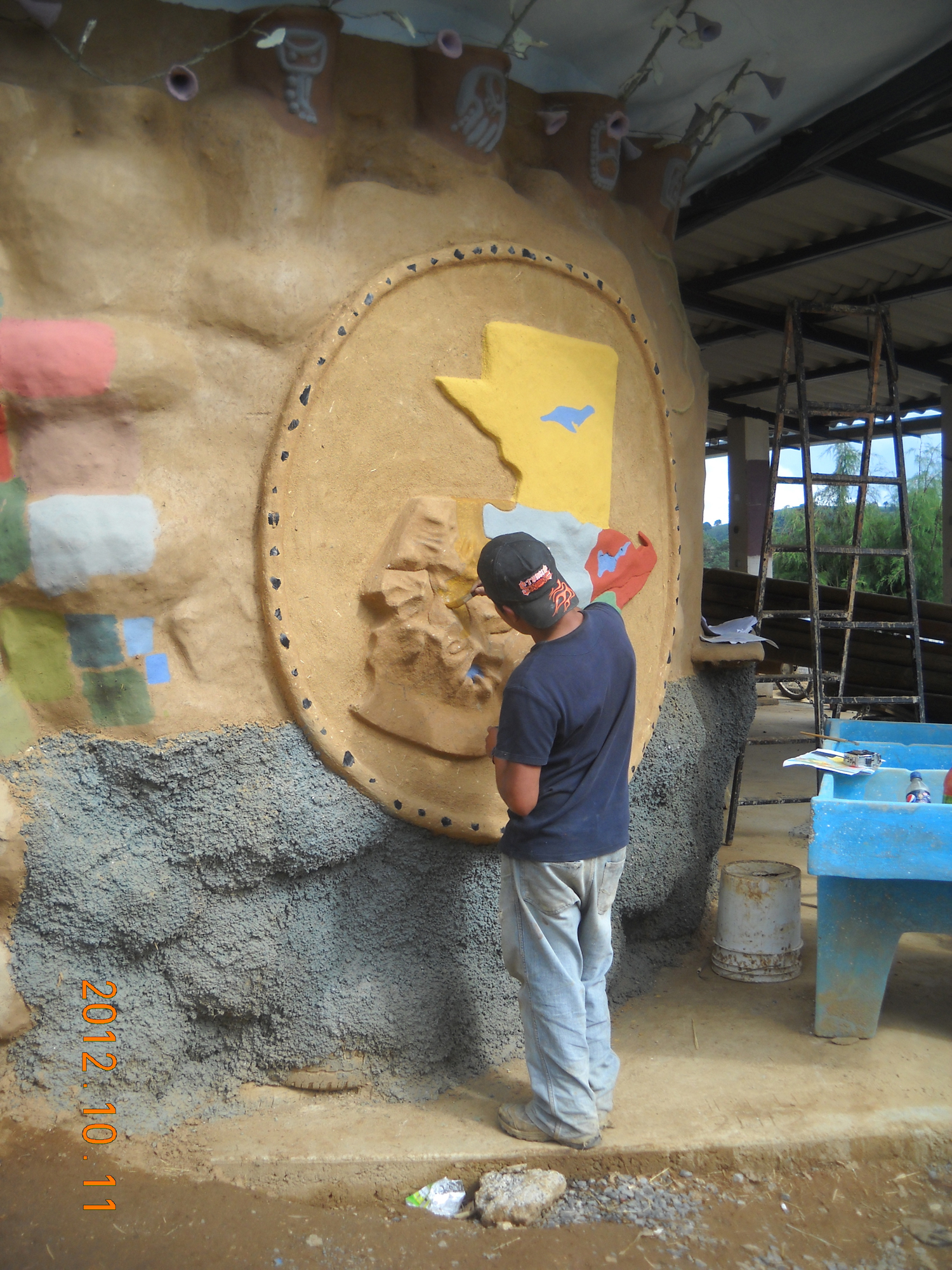
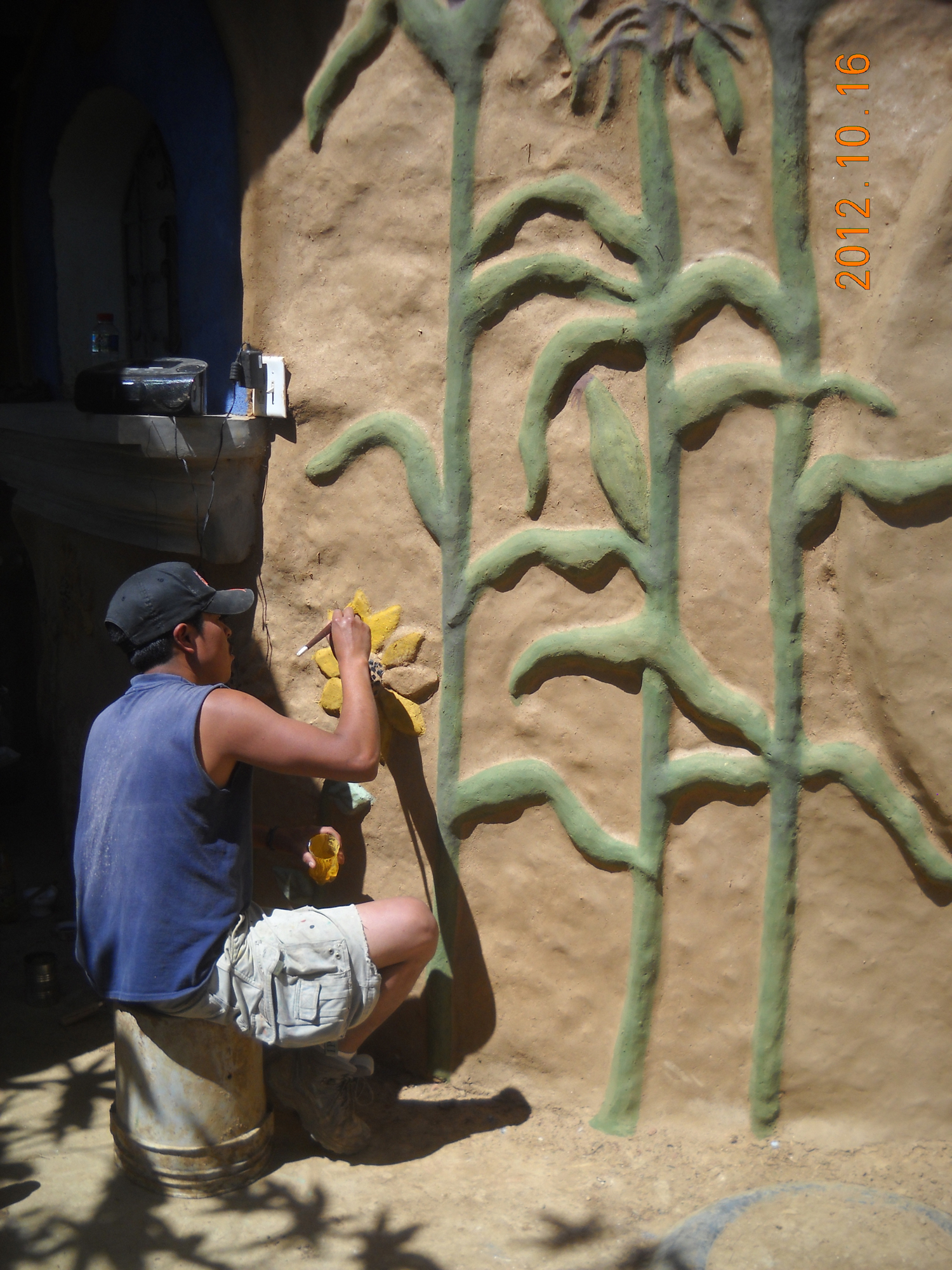

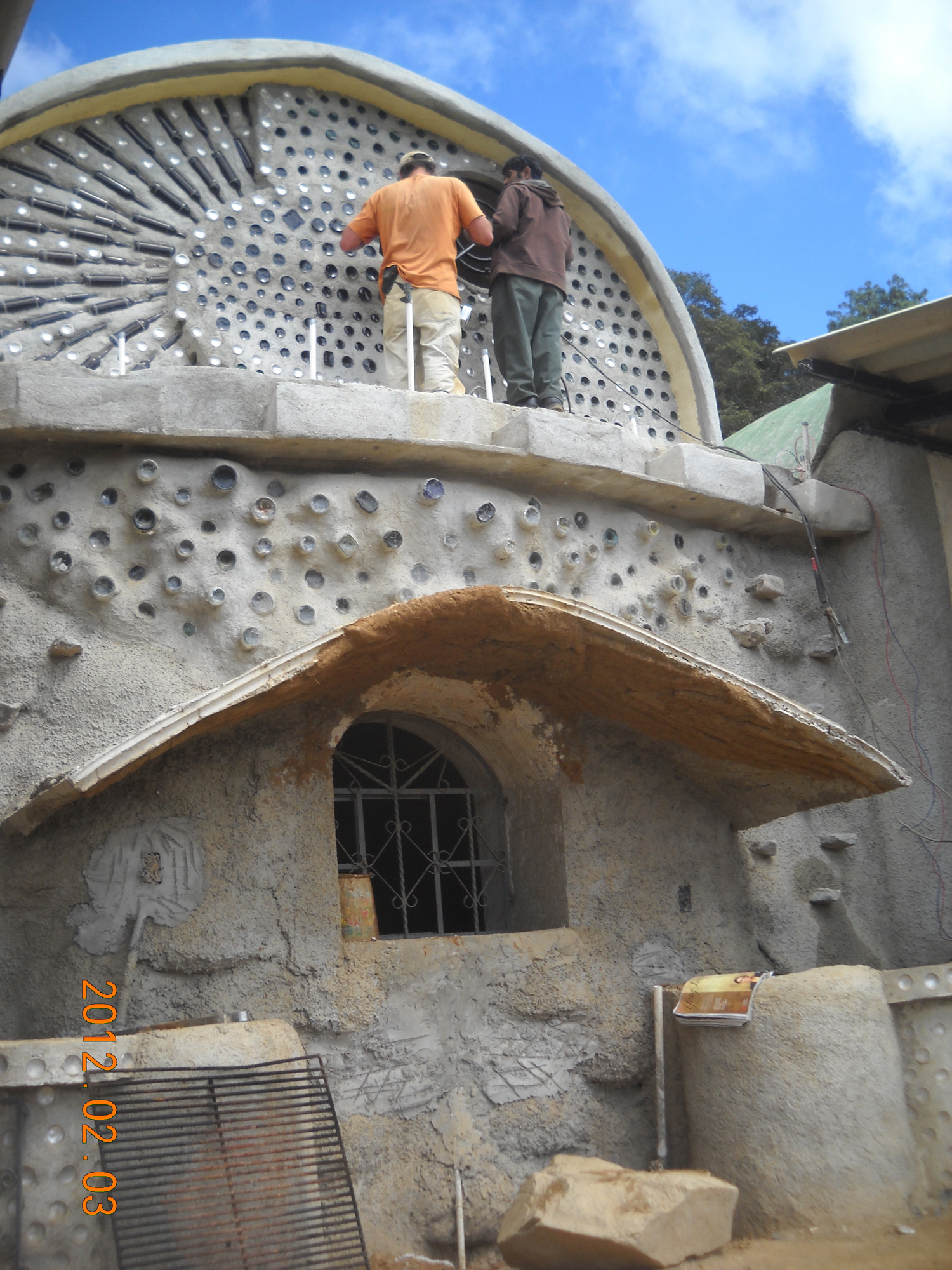
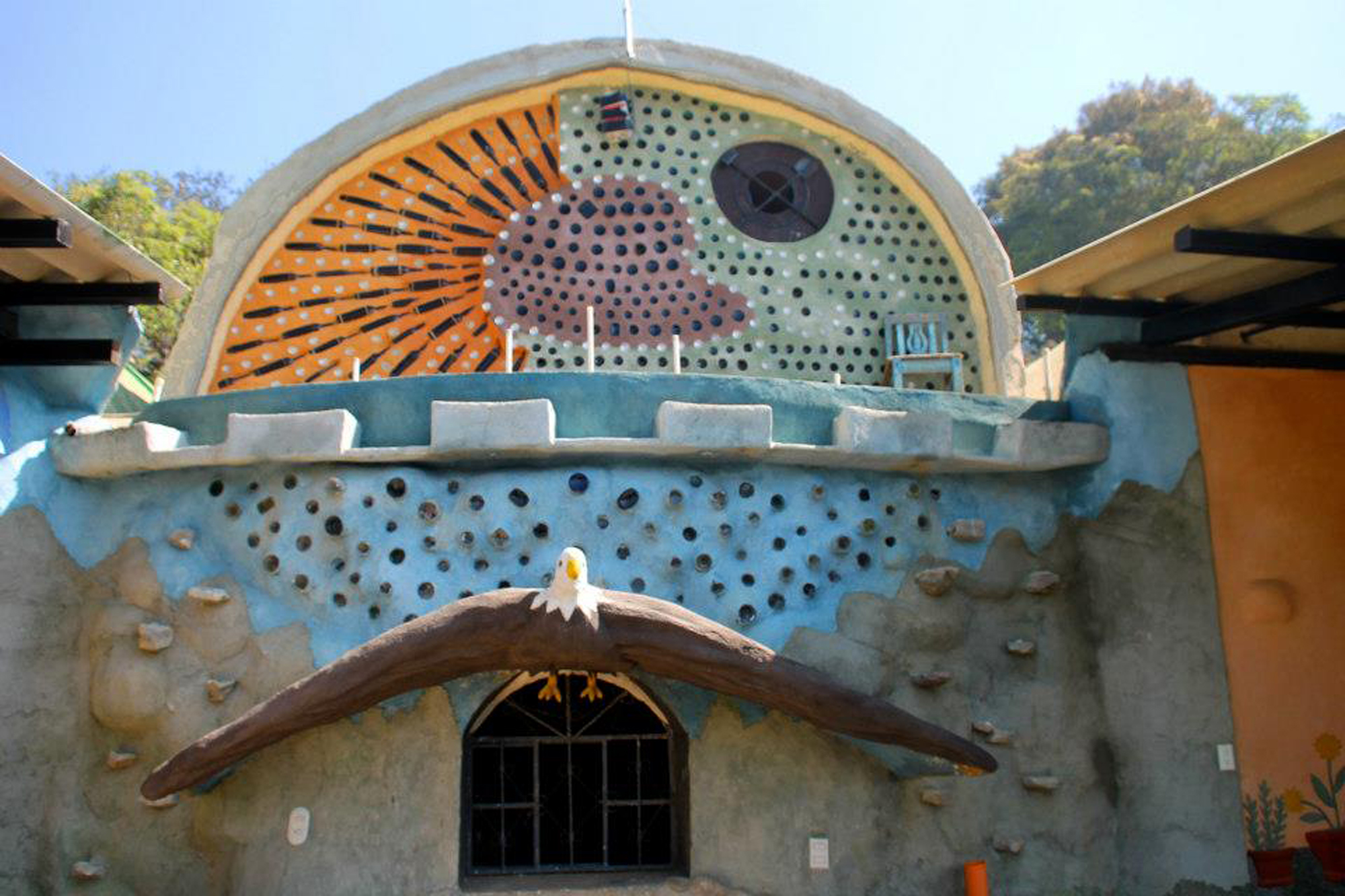

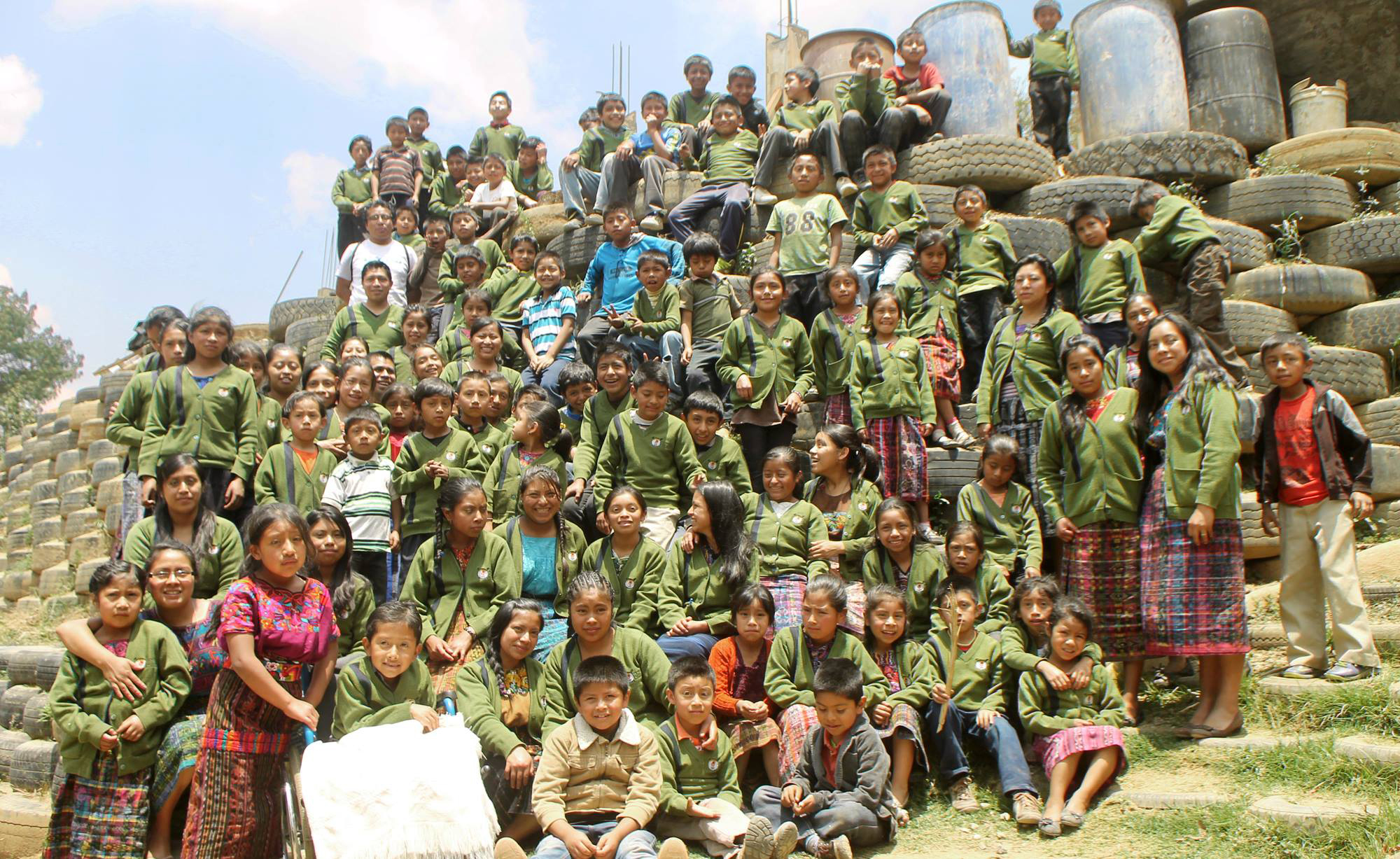
Full Process -
Images